CASE STUDY: Cyclife Sweden AB
Control over hours and a better utilisation rate with an integrated platform
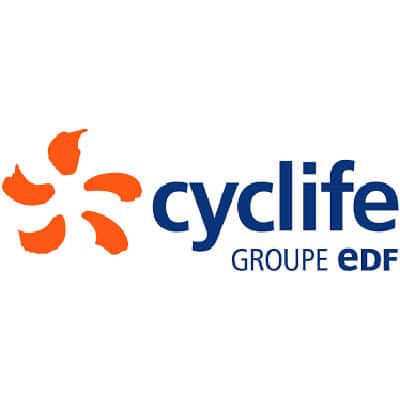
Cyclife Sweden AB handles and volume-reduces low-level radioactive waste (metal, liquids, combustible waste and radiation sources) for companies within the nuclear power industry and other industries – with customers in both Sweden and Europe.
Cyclife Sweden is a part of EDF Groupe (Électricité de France), one of the world’s largest energy companies, partly owned by the French State.
Cyclife Sweden has 100 salaried workers and a number of hourly-paid employees at the waste facilities in Studsvik, just outside of Nyköping.
“For Cyclife, the benefits of having a fully digitalised platform and integration to various business systems such as SAP and payroll – without human intervention and paperwork – are great. With exact job and project hours, we can provide our customers with offers that correspond to the actual production time”.
– Urban Lind, IT Manager, Cyclife
The challenge
- ^Too many manual processes related to time reporting and absence management
- ^Insufficient overview of use of time on external projects for follow-up
- ^Insufficient overview of the production chain to be able to make the right scheduling, planning and follow-up
Success criteria
- ^An integrated solution for both production and project reporting as well as payroll-related data
- ^A solution that covers all salaried workers and hourly-paid employees in the Swedish part of the company
- ^All employees have a mobile phone for all reporting – even in production
Key functionality
- ^ProMark 365 Cloud Individual with Time & Attendance reporting
- ^Job and project registration
- ^Registration via mobile app and terminals
- ^Integration with SAP Business One and Visma Agda PS payroll system
- ^SuperuserService from ProMark
Outcomes
- ^Simpler payroll process, without manual work
- ^Managers have overview of employees’ attendance and absence, which simplifies working time scheduling
- ^Collection of hours per job and project provides overview of production time and all internal working time for follow-up and forecasting
Primary results
- ^Correct salary on time
- ^Optimised scheduling with control of working hours and overtime limits
- ^Exact job and project hours contribute to a better utilisation rate
- ^Predictable costs in the IT budget
Talk to our experts
Learn how ProMark can help you optimise your workforce, improve productivity and generate savings. Schedule a demo or call sales to get an introduction.
Discover more
Our latest cases